Time- and battle-tested, lean manufacturing principles have been a staple of the industrial factory for decades, so significantly that productivity-starved construction companies have been borrowing a page from that playbook (we’ll get more into that below). But as to “agile,” that’s a relatively new term.
Best known to be practiced among the tech-focused startups of Silicon Valley, the methodology behind agile software development or agile project management may seem alien to the construction trades—just about as unfamiliar in concept as the practitioners of them may seem inaccessibly geographically distanced. But in fact, the principles they’re built on are fundamentally comparable and applicable to construction companies looking to increase their productivity despite facing organizational challenges (namely, growing construction labor shortages).
In this article, thus, we’ll cover a few important considerations:
- Lean manufacturing principles—what they are, why and how they’ve been applied in the industry in form of lean construction.
- Agile software development processes and methodologies—what they are, the important principles and functional similarities they share with the construction industry, and how companies in this space may look to these processes and methodologies when implementing their own procedures in order to boost productivity with the cards they’re dealt.
Lean Construction Definition and History: How to Apply Lean Manufacturing in Construction
The word “lean” might bring to mind prominent martial artist Bruce Lee, who unlike traditional body builders and Mr. Olympia honorees who bulk up, practiced a different kind of strength training, becoming as a result physically strong but not bulky and unwieldy.
Similarly, lean thinking is rooted in purpose-driven principles, to create strength through a unified focus and an inextricably linked production system designed to maximize efficiency and productivity toward delivering on that focus.
How has lean manufacturing changed throughout history?
Lean thinking can be traced back to the automobile manufacturing industry of the 1930s. Debatably, Henry Ford was the first person to adopt an exhaustive production process, able to turn around inventory in mere days. Ford’s Achilles heel in those early days was not flow but limited variety. Though high output/quantity of the same product was doable, introducing variations (new models, different colors, etc.) hadn’t yet been mastered.
Enter: Kiichiro Toyoda (founder of Toyota Motor Co). Toyoda, whose family had roots in the textile industry, had a passion for machines, and developed looms to help make weaving garments more streamlined through automation. Toyoda realized that revising Ford’s system with a couple important innovations (shifting the focus of a manufacturing engineer from individual machines to the flow of the product through the entire process) could result in something magical and seemingly out of reach becoming feasible: “low cost, high variety, high quality, and very rapid throughput times to respond to changing customer desires.”

It all starts with generally 5 principles of lean manufacturing:
- Define value: It’s important to understand the needs, and wants, of the customer to ensure their expectations and satisfaction are met, and friction is minimized. Generally, this could be in the form of user interviews, surveys, or demographic information to ensure you discover insights about what your customers will find valuable. At Milwaukee Tool, we’re proud that defining value has been an integral part of our story. We spend countless hours on jobsites meeting our end users on their turf and developing a firm understanding of their needs, desires, as well as their pain points with the current solutions in the industry—using these insights to drive product development and engineering.
- Map value stream: In this step, customer value is used as a reference point and situated in relation to the overall product goal setting and planning. It’s during this stage that “wastes” (non-value adds/unnecessary features) are eliminated while value adds are incorporated and perfected.
- Create flow: After the waste is removed from the value stream, additional actions (such as reconfiguring production steps, leveling out workload, creating cross-functional departments) are taken to ensure there’s a smooth completion of the remaining tasks.
- Establish pull system: Just like a tool crib manager uses One-Key to ensure that equipment arrives in time for the job (and avoids costly downtime), pull-based systems in manufacturing ensure inventory-related snags are averted. Pull-based planning makes certain that the relevant information and necessary materials are made available to the team to create a smooth workflow. This allows for “just-in-time” delivery and manufacturing, where products are created perfectly to spec and in time and in the desired quantities, similar to how grocery store inventory is replaced right as customers take products off the shelf (avoiding overfill and putrid spoiling as products remain on the shelves unpurchased).
- Pursue perfection: Also called continuous improvement or Kaizen (a Japanese concept and part of the Toyota Production System we discussed above), pursing perfection is just as it sounds; creating an organisational culture where employees strive toward perfection while delivering products inextricably linked with customer needs.
Lean construction definition
Studies have shown the construction industry to represent “large amount of waste activities,” much higher than typically experienced at a manufacturing plant:
- Excessive material handling
- Rework
- Design errors
- Conflicts between trades
- Conflicts between other contractors
- Ineffective supply chains
Any one or combination of these could result in a costly project overrun, but that’s where the lean principles we discussed above come in.
Lean construction, as defined by the Lean Construction Institute, “extends from the objectives of a Lean production system—maximize value and minimize waste—to specific techniques, and applies them in a new project delivery process.”
Today, with the advent of digitisation, Deloitte estimates lean technologies can reduce annual costs by 15% and improve overall equipment effectiveness by 11%.

At the core of this philosophy is the customer. Lean aims to precisely identify, target, and deliver on customer value while streamlining workflows and processes in order to maximize productivity.
To start, establishing a high-trust culture is mission critical to understanding customer needs and determining expectations. Leading with transparency, and fostering collaboration, can help assure miscommunication, and expensive rework, is averted.
From here, what are some techniques that can be applied to your delivery system (it’s all about optimizing flow!) in service of prioritizing customer value?
- The importance of construction quality management for contractors should not be understated. BIM software can help preview jobs and mitigate risk while streamlined design-build approaches as well as prefabricated construction and modular construction methods can help with scheduling, improve quality control, and limit materials’ exposure to environmental factors like inclement weather that may otherwise cause damage.
- Integrated construction software keeps busy cross-functional teams on the same page with data-driven approaches that help baseline and set actionable goals and KPIs.
- Construction drones can help with anything from surveying land to performing safety inspections to asset locating and providing real-time progress updates.
Agile Software Development Processes and Methodologies
There’s a reason that the agile methodology is so common in software development among Silicon Valley tech startups. Ever meet anyone who has worked for a startup? The common trope: underpaid, overworked, compensated in stock options.

These hard-pressed engineers need to set priorities and create efficiencies in order to deliver valuable features while not getting bogged down in the backlog.
Waterfall, say what?
In traditional software development, the process looks similar to that of a waterfall. In a waterfall, stream or river water flows over a vertical drop. Once you fall over the edge, there’s no turning back as you plunge downward.

Similarly, waterfall software development is a linear approach that follows a sequence of events: requirements are gathered, design commences, designs are coded and tested, any bugs that are found are squashed, and then finally the finished product (software update) is deployed. Each of these events represents a distinct stage, with each new stage finishing before the next stage can begin.
Similar to the “waste activities” we discussed above of experienced in the construction industry, the waterfall model in app development invites plenty of room for inefficiency—as a framework with excessive rigidity, limited flexibility, it makes addressing customer concerns and last-minute requests challenging.
Defining agile software development in simple terms
Agile, meanwhile, is an iterative, team-based approach to software development that emphasizes rapid delivery of functional products in a short period of time (known as sprints). Like the lean manufacturing principles—namely, Kaizen (continuous improvement)—subsequent batches are planned in cyclical schedules.

Advantages of agile over waterfall:
- Customers/users of app have frequent and early opportunities to see features that are being worked on, provide feedback, and request changes. With One-Key, we actively recruit and advertise alpha and beta releases of our major features (some recent examples include multi-user and tool kitting).
- Development as a result is more user-focused.
- Fixed, predictable schedule and delivery. With One-Key, we’re currently on a two-week release cycle, so you can expect a new app update every two weeks (usually bug fixes, performance improvements, with bigger features spread out).
- Improved quality and continuous improvement. By breaking into manageable units, product teams can focus on high-quality development, testing, and collaboration to deliver valuable features, and making those valuable features better and better based on user feedback. Currently, the One-Key team has dedicated product teams that work on location and tracking features, major features (like multi-user and tool kitting), and continuous improvement (i.e., how can we make our app better, easier to use, based on user feedback).
- Allows for change. Transparency and collaboration between product teams allows for refinement and reprioritization, just like lean contractors may use various tools like collaborative BIM and prefabricators to help improve scheduling.
Similarities Between Lean Construction and Agile Software Development Abound
On the One-Key team, we have the unique privilege working for a large power tool manufacturing company on a mobile- and web-based software application, which in a weird but awesome way is kind of like working for a small startup within the larger organization. As a result, we’re able to be exposed to lean manufacturing principles, rapid prototyping, and product development, while also developing our app within the agile framework.
With these considerations front of mind, there are some definite parallels between lean construction and agile software development we felt compelled to make:
- both focused on providing value
- both emphasise improving flow/efficiency
- both rooted in a framework of continuous improvement
I’ll leave you with two thoughts:
- While as Bruce Lee (callback!) was focused on being lean and mean, not buff and bulky, a perhaps even more applicable sentiment for the construction industry is how a famous design principle, “form follows function” conceived by architect Louis H. Sullivan, became the foundation for the modern skyscraper. As it sounds, central to Bruce Lee’s philosophy, is the idea that needless ornamentation should be stripped away in favor of that which drives purpose.
- A powerful and valuable attribute, being agile requires being able to create and quickly adapt to change, like a cat caught off guard being able to twist its body in midfall to land perfectly on its feet.
Focusing on these principles—delivering true value in place of non-value adds, and being able to quickly respond to change—is critical to your success. Echoing through these principles is the voice of the customer, their needs, and the values they seek, driving you to create and adapt, and earn more business while your laggard competitors fail to evolve.
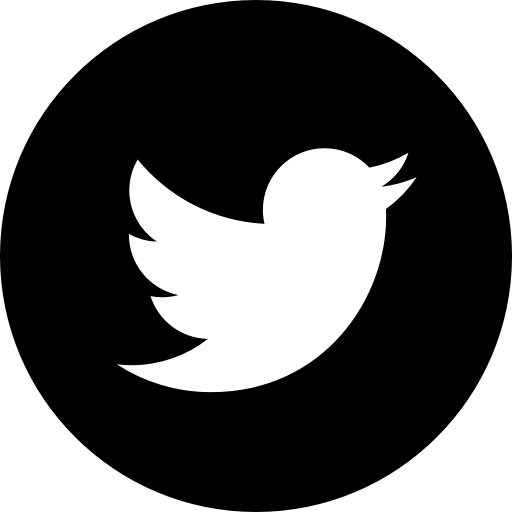